Introduction
En orthopédie il existe déjà une utilisation marquée de la 3D et de nombreuses sociétés se sont déjà positionnées pour la réalisation de pièces ou d’appareillages d’orthopédie. Les appareillages sont en général liés à la morphologie des personnes et donc à caractère uniques. De plus en plus de matières 3D sont aussi homologuées contact cutané et ce qui étend le champ des possibles. Les appareillages peuvent être instrumentés avec des dispositifs de captage de données pour les professionnels de la santé.
Le cas que nous allons décrire est issu de l’utilisation de dispositifs à base de capteurs pour la rééducation orthopédique. Il est lié à une application bien connue de la 3D qui est la réparation de pièce(s) pour des petites séries voire pour des pièces uniques dont le moule matrice a disparu. Ce cas intervient directement dans le cadre d’un dispositif de suivi digital orthopédique préventif ou réparateur des sportifs ou de l’ensemble des personnes présentant des problèmes d’entorse à la cheville.
La demande est issue d’un kinésithérapeute travaillant pour la structure CKS Sauvegarde à Lyon . Nous tenons à le remercier chaleureusement pour la confiance qu’il nous a témoigné tout au long de l’étude car ce n’était pas gagné d’avance !
Contexte
Un des dispositifs du centre de kiné du sport de la Sauvegarde permettant la réalisation d‘exercices de rééducations, comme le renforcement et la proprioception pour des entorses de cheville est commercialisé par la société Myolux. Il est équipé d’un capteur ou centrale inertielle commercialisé par Shimmer. Ce type de capteur clipsé sur un chausson mobile est une réelle avancée technologique dans le domaine. La société Myolux propose à partir d’un logiciel de traitement des données initiales du patient d’adapter les exercices de rééducation ou de renforcement en fonction des personnes. Les progrès se mesurent dès les premières séances.
Cet appareillage s’est trouvé cependant hors d’usage parce qu’une petite pièce amovible en polyamide qui accueille le capteur avait cassé. Il était donc très dommageable de ne pas pouvoir utiliser au CKS Sauvegarde un tel dispositif de plusieurs milliers d’euros juste à cause de la rupture d’une petite pièce intermédiaire. En échangeant avec le Kiné, nous avons pensé que l’impression 3D pouvait apporter une réponse adaptée pour remédier au manque de pièces amovibles de substitution. Le challenge de pouvoir remplacer sa pièce défectueuse à partir d’une impression 3D était devenu une évidence et était lancé pour PolyPoc.
Mise en place de l’impression 3D de support de capteur
Nous avons donc analysé la géométrie de la pièce existante et conclu que le principal défi serait le respect des côtes de la pièce et donc la précision de l’impression si aucune erreur n’est présente sur le fichier CAO. Il fallait une précision de 1/10 pour des ergots de calage de 2mm pour réaliser la pièce fonctionnelle demandée. L’impression 3D en cuve de type DLP ou SLA permettra de répondre à ce genre d’exigence qualitative sans traitement de surface alors qu’il est difficilement envisageable de pouvoir réaliser ce genre de pièce avec la même précision par impression 3D fusion filamentaire (FFF) sans lissage de finition.
2 stratégies pour réaliser la conception de la pièce
-Une des options de conception de la pièce est de réaliser un travail de CAO à l’aide d’un scan pour obtenir les caractéristiques géométriques exactes de la pièce à réparer sous forme de fichier numérique directement transposable à une imprimante 3D.
-Une deuxième option consiste à réaliser la pièce à partir d’un fichier imprimable en 3D issu d’un travail de réingénierie représentant la pièce conçue pour de l’impression 3D et non plus pour un procédé de fabrication par moulage.
C’est la deuxième option que nous avons choisie mais nous étudierons sur cette preuve de concept ce qui est le plus rentable, et rapide. En effet à partir d’un scanner professionnel il est clair que l’on peut obtenir immédiatement une approche volumétrique exacte de la pièce et proposer une solution de dépannage immédiate. L’approche dessin (DAO) que nous avons choisi, permet de bien réfléchir également aux fonctionnalités de la pièce et finalement de redésigner un modèle adapté et plus robuste que celui proposé par le fournisseur sans forcément respecter la géométrie exacte du modèle initial. On conçoit ainsi un objet fonctionnel respectant certains critères de l’impression 3D.
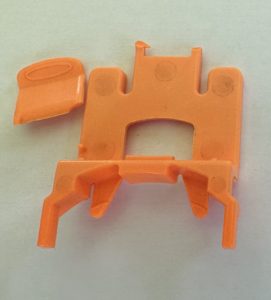
Réalisation
Nous avons consacré quelques heures à la réalisation du dessin de la pièce et proposé une ébauche à notre client. Il s’avère que la première pièce imprimée en 3D réalisée à partir d’une résine PU-acrylate à 385nm d’irradiation (2,5 secondes par couche) a également subie une rupture très rapide au niveau de la languette.
Nous avons pensé que c’était plus un défaut de dessin de la pièce avec des points de faiblesse au niveau de la jonction des volumes créés qu’un problème de faiblesse du matériau après photoréticulation lors de l’impression 3D . La deuxième préparation du dessin de la pièce 3D s’est révélée gagnante avec une bonne résistance de la languette après impression 3D. La pièce testée a été validée par le kiné sur le dispositif Myolux et est donc opérationnelle.
